Calcul des besoins industriels (MRP)
Le « Calcul des besoins industriels » ou Material Requirements Planning (MRP) est une méthode de gestion de la production et des stocks qui permet de déterminer les besoins en matières premières et en composants nécessaires pour produire un certain nombre de produits finis. L’objectif principal du MRP est d’assurer que les matériaux et composants sont disponibles pour la production. En parallèle, il a pour objectif de minimiser les niveaux de stocks et de s’assurer que les délais promis aux clients sont respectés.
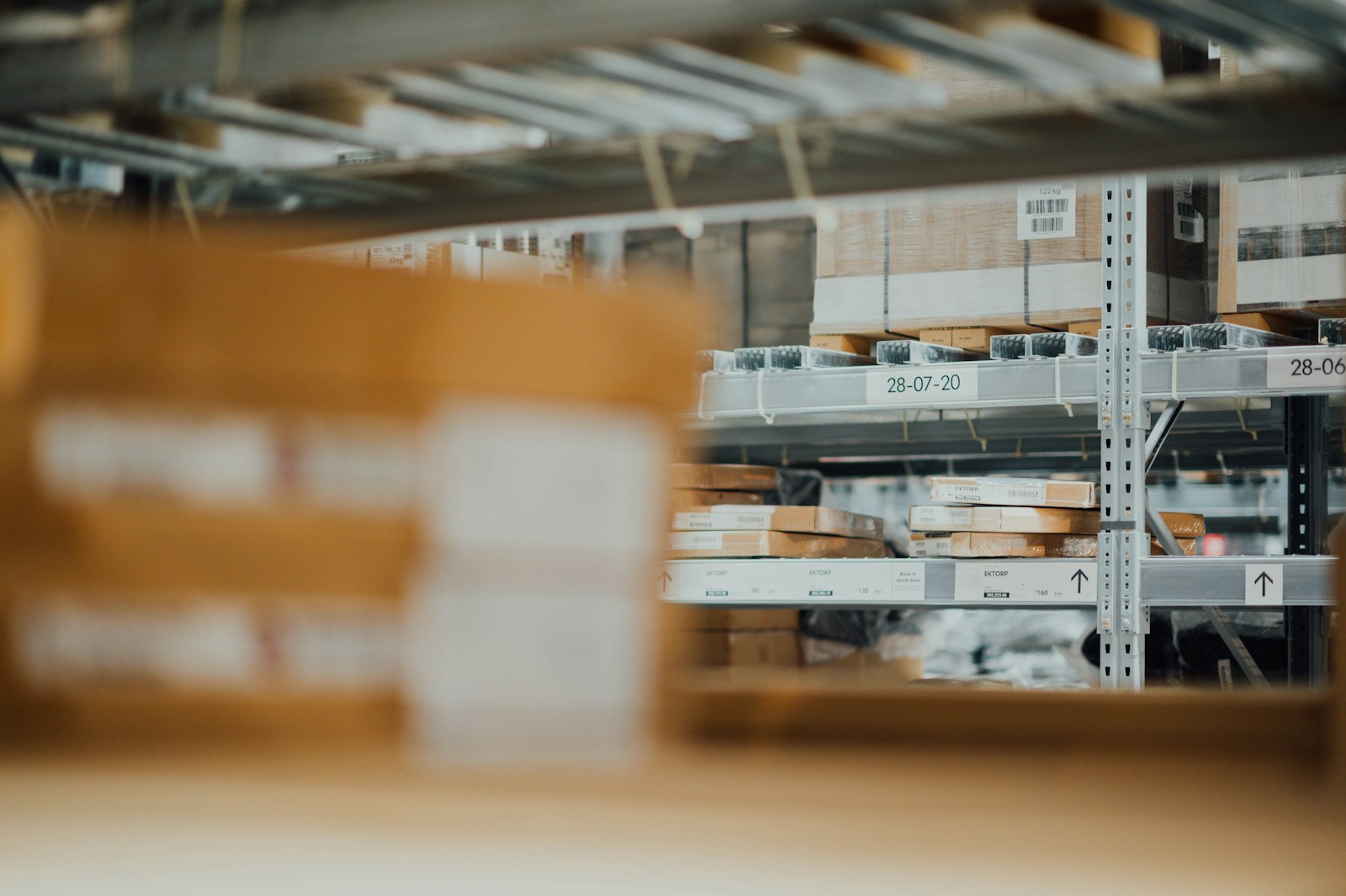
A quoi sert le calcul des besoins industriels ?
Le calcul des besoins industriels permet de déterminer avec précision les quantités de matières premières, de composants et de produits finis nécessaires pour répondre à la demande de l’entreprise, tout en minimisant les coûts et les délais. Grâce à des outils de planification avancés, les industriels peuvent anticiper les fluctuations de la demande, éviter les ruptures de stock et améliorer leur efficacité opérationnelle. En somme, le calcul des besoins industriels est un levier stratégique fondamental pour renforcer la compétitivité des entreprises industrielles et optimiser leur rentabilité.
Le « Material Requirements Planning » (MRP) est une méthode de gestion de la production et des stocks qui permet de déterminer les besoins en matières premières et en composants nécessaires pour produire un certain nombre de produits finis. L’objectif principal du MRP est d’assurer que les matériaux et composants sont disponibles pour la production, tout en minimisant les niveaux de stocks et en s’assurant que les délais promis aux clients sont respectés. La mise en place d’un MRP favorise ainsi une meilleure gestion des stocks (en évitant les surstocks et les ruptures de stock). A court terme, l’optimisation des besoins via le MRP se traduit par une réduction des coûts opérationnels grâce à l’optimisation de la chaîne d’approvisionnement. Enfin, en fluidifiant la production et en la rendant plus efficace grâce au MRP, les industriels permettent d’activer tous les leviers stratégiques qui leur permettront d’augmenter la satisfaction de leurs clients.
Pourquoi automatiser le MRP ?
L’automatisation du MRP présente de nombreux avantages pour les entreprises industrielles. Les entreprises peuvent par exemple réduire les erreurs humaines tout en accélérant les calculs complexes nécessaires à l’estimation des besoins en matières premières et en composants. De plus, l’automatisation permet une plus grande flexibilité lorsque les besoins évoluent, que les clients modifient leurs commandes, etc. Il est ainsi possible de créer des flux de travail automatisés, qui répondront à chaque modification de votre programme de vente et qui réajusteront le calcul des besoins industriels en temps réel.
Qui peut bénéficier d’un calcul des besoins industriels automatisé ?
Industriels, artisans, commerçants, sociétés de services… Dès lors qu’il y a des transactions de stocks, des achats et des ventes de matériels, le calcul et la planification des besoins deviennent des éléments prépondérants dans la stratégie de développement à court / moyen terme. La plupart du temps, ce calcul est chronophage mais s’avère relativement peu complexe, dès lors que tous les enjeux et les éléments (commandes clients, ordres d’achats, stocks existants et en transit, ordres de fabrication planifiés, etc.) entrent en ligne de compte.
Automatiser le MRP devient ainsi un enjeu stratégique, au même titre que l’automatisation d’une ligne de production. Planifiez vos commandes dans la journée et laissez le système calculer et ajuster tous les besoins pendant la nuit. Le matin suivant, vous bénéficiez ainsi de toutes les informations nécessaires pour préparer sereinement vos prochaines commandes !
Comment mettre en place une solution MRP automatisée ?
1. Le plan commercial
Centré sur les activités commerciales, le plan commercial définit les ventes prévisionnelles sur une période donnée. Ce plan de vente va naturellement créer des besoins industriels et sera à la base du calcul du MRP.
2. Le plan directeur de production
De son côté, le plan directeur de production s’appuie sur les ventes prévisionnelles et définit les volumes de production nécessaires pour répondre aux besoins commerciaux (=ventes). Cette vision consiste à définir combien il faudra produire ou déstocker de produits finis pour répondre aux commandes des clients.
3. Le plan de charge
Pour sa part, le plan de charge va définir au plus fin quelles pièces il faut produire, en quelles quantités et à quelle date pour honorer les commandes clients, tout en minimisant les coûts de stockage et d’approvisionnement. En pratique, pour chaque ordre de fabrication défini dans le système, le plan de charge définira les stocks minimaux pour chaque pièce, les dates de réapprovisionnement, etc.
Les sources : ERP (Enterprise Resource Planning), MES (Manufacturing Execution System) et PLM (Product Lifecycle Management) de l’entreprise.
Les ventes sont saisies par les équipes dans l’ERP. Les délais de production sont connus par le MES et le PLM définit les nomenclatures de fabrication. Les équipes en charge de la planification doivent ensuite décider comment seront fournis les ordres de vente en produits finis (depuis les stocks existants, en fabrication directe, etc.).
Passez au MRP maintenant avec nos experts industriels !
Le MRP automatisé: la solution de Datavizin
Les intrants de production, les stocks disponibles et les achats de matériel, les capacités de production et les commandes clients sont extraits des différents systèmes source ou de l’ERP si toutes ces informations sont centralisées.
Le MRP va ensuite construire le plan de production et estimer les besoins en répondant à plusieurs questions :
– quelles sont les quantités qui ont été promises aux clients et pour quelles dates ?
– quel est l’état des stocks à l’instant T ? Quelles pièces ont été commandées auprès des fournisseurs et quand arriveront-elles ?
– combien de temps faut-il pour fabriquer nos produits finis ?
– quel sera le taux prévu d’occupation des machines par rapport aux prescriptions ?
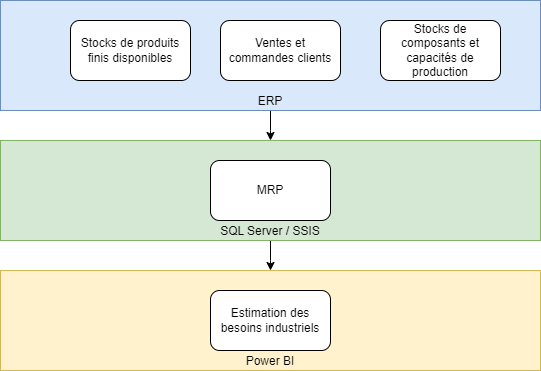
Notre solution de calcul des besoins industriels s’appuie sur 3 piliers majeurs :
– les systèmes sources de l’entreprise (ERP, CRM, MES, etc.) qui hébergent les données essentielles
– une série de programmes et paquets SSIS (SQL Server Integration Services) qui vont agréger, préparer et consolider les données des systèmes sources
– une suite de solutions de Business Intelligence (tableaux de bords, rapports, etc.) accessibles depuis Power BI Desktop ou Power BI Server.